On May 1, Apple warned customers that ongoing tariffs tied to former President Donald Trump’s trade policies could drive up costs by as much as $900 million by the end of the second quarter, which ends in June.
The tech giant stated that the tariffs on imported goods significantly impacted its bottom line, though CEO Tim Cook emphasized that Apple had taken steps to mitigate the effect by adjusting supply chains and inventory management.
Despite the steep projected cost increase, Cook noted during a conference call that the company experienced only a “limited impact” in the second quarter, thanks to these strategic adjustments. He added that Apple is working on long-term solutions to further reduce exposure to tariff-related costs.
Apple expects to see a massive increase in costs for the end of the 2nd quarter (Cheng Xin/Getty Images)
For the quarter ending in June, he stated: “Assuming no changes to current global tariff rates, policies, or applications—and no new tariffs are introduced—we estimate an additional $900 million in costs.”
He also noted that most iPhones sold in the U.S. will originate from India, while the majority of iPads, Macs, and Apple Watches will be manufactured in Vietnam. This shift reflects the company’s strategic investment in relocating production outside of China.
Cook explained: “We have a complex supply chain, and there’s always risk involved. What we learned some time ago is that concentrating everything in one location poses too great a risk.”
However, experts caution that despite these moves, the increased costs could still trickle down to consumers. Jacob Bourne, an analyst at Emarketer, remarked: “Apple’s proposed manufacturing shift to India raises critical questions about execution timelines, production capacity, and inevitable cost increases—which may reduce margins, be passed on to consumers, or lead to a combination of outcomes.”
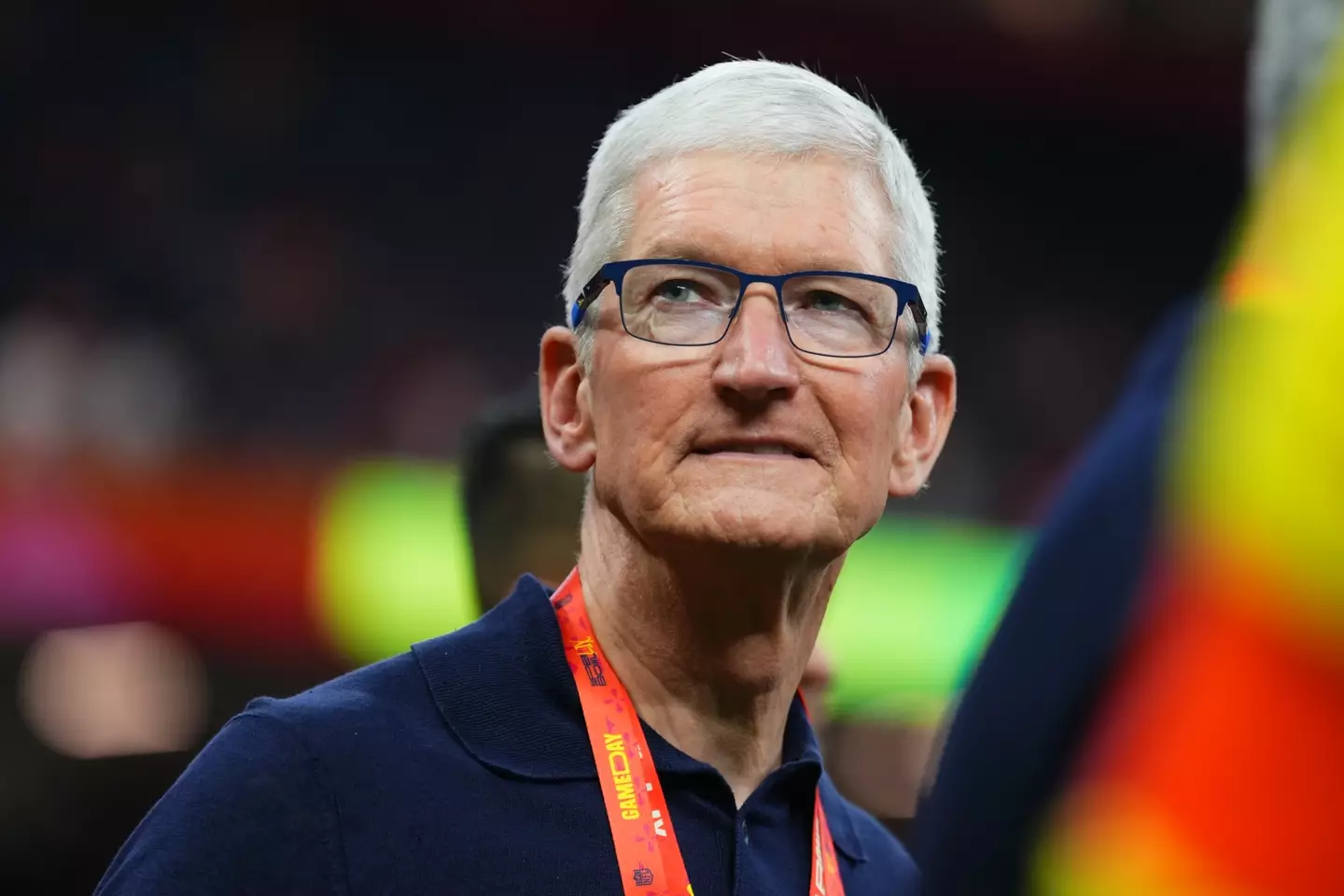
Tim Cook explained Apple had enacted plans to limit the impact of tariffs (Cooper Neill/Getty Images)
Following Trump’s initial tariff announcement on April 2, Dan Ives, an analyst at Wedbush Securities, warned that in a worst-case scenario, the next iPhone could cost as much as $3,500.
This would be a significant jump from Apple’s current top-tier model, the iPhone 16 Pro Max, which retails for $1,199.
“For U.S. consumers, the idea of a $1,000 iPhone—one of the best-made consumer products on the planet—would vanish,” Ives said. “It underscores our point: if consumers want a $3,500 iPhone, we should build them in New Jersey, Texas, or another U.S. state. But at $1,000, making iPhones domestically is a non-starter.”